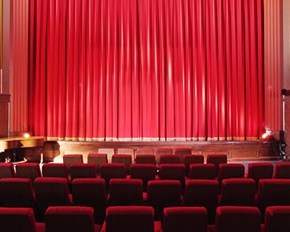
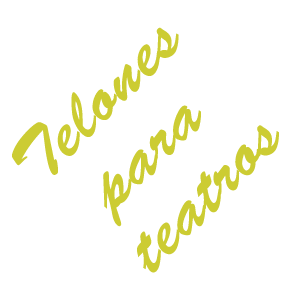
Alzadores infantiles para butacas
En Eurotelon contamos con un amplio catálogo de accesorios para salas de cine y teatro. Disponemos de todo lo necesario para equipar su sala por completo, desde butacas, moquetas o cortinajes hasta alzadores infantiles.
Somos distribuidores de la prestigiosa marca Korflip, líder en la fabricación de alzadores infantiles para butacas de cine y teatro, diseñados para ser empleados en cualquier tipo de butaca tradicional de forma segura y cómoda.
Con el uso de Korflip, los niños pueden disfrutar en el cine o en el teatro, ya que están diseñados para adaptarse a cualquier tipo de butaca. Su diseño contiene numerosas medidas de seguridad, tales como: base antideslizamiento, asiento ergonómico, aristas pulidas, perímetro prominente y superficie antideslizamiento. Además, los alzadores son duraderos, resistentes y fáciles de mantener, ya que son muy resistentes al impacto y fáciles de limpiar gracias al PVC inyectado de última generación empleado en su fabricación.
Con los alzadores infantiles para butacas Korflip, podrás equipar por completo tu sala de cine y hacerla accesible para todo tipo de público.
Realizamos envíos a toda España, solicite presupuesto sin compromiso, en Eurotelon somos distribuidores oficiales de Alzadores infantiles para butacas Korflip.
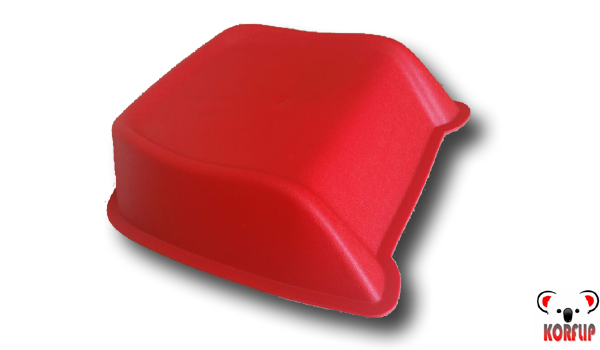
Vídeo mostrando embalaje de los alzadores infantiles para butacas que comercializa Eurotelon para Cines y Teatros